Understanding the Benefits of Silicone Membrane for Vacuum Forming
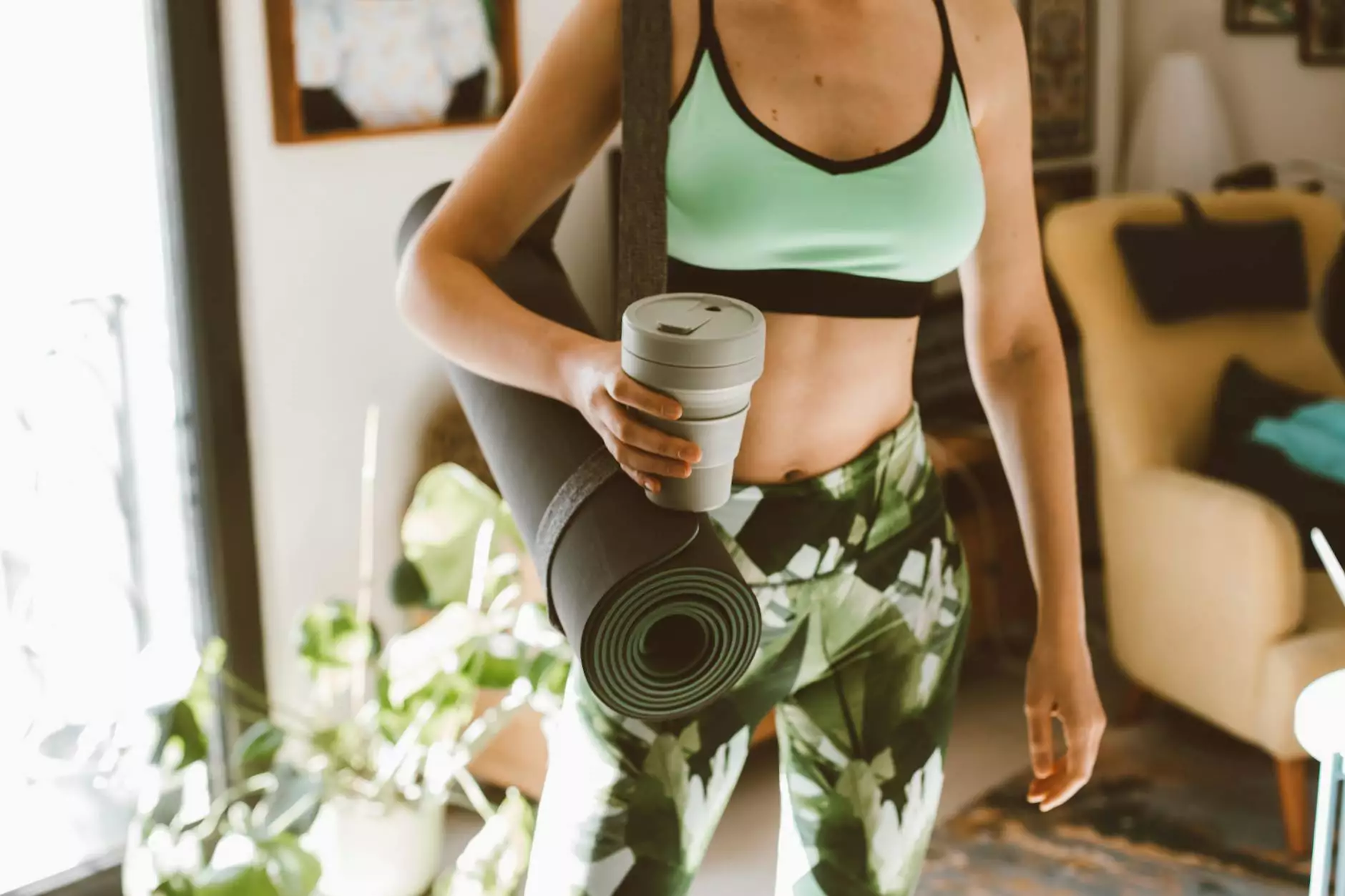
Introduction to Vacuum Forming
Vacuum forming is a widely used manufacturing process that involves shaping plastic sheets over a mold. It’s efficient, cost-effective, and allows for a wide variety of applications across multiple industries, including automotive, aerospace, and consumer products. As a crucial part of this process, the silicone membrane for vacuum forming plays an essential role in ensuring quality and precision in the final product.
The Role of Silicone Membranes in the Vacuum Forming Process
A silicone membrane serves as a flexible, durable barrier that connects the vacuum source to the forming material. This membrane is responsible for creating the vacuum needed to pull the plastic sheet around the mold, thereby ensuring that the material conforms perfectly to the shape of the mold.
Advantages of Using Silicone Membrane
- High Temperature Resistance: Silicone membranes can withstand high temperatures without losing structural integrity, making them ideal for various molding scenarios.
- Flexibility: The inherent flexibility of silicone allows for a tighter seal, which results in better vacuum efficiency and higher-quality molded products.
- Longevity: Silicone membranes are resistant to wear and tear, contributing to lower maintenance costs and prolonged usage in manufacturing setups.
- Chemical Resistance: These membranes are less likely to degrade when exposed to various chemicals, making them suitable for diverse environments.
- Customizable Thickness: Silicone membranes can be manufactured in various thicknesses to cater to specific applications and requirements.
Applications of Silicone Membranes in Various Industries
The versatility of silicone membranes for vacuum forming spans numerous sectors, including:
1. Automotive Industry
In the automotive sector, silicone membranes are extensively used for forming dashboard components, panels, and under-the-hood parts. Their ability to maintain high performance even in demanding environments ensures that automotive components meet stringent industry standards.
2. Aerospace Industry
The aerospace industry requires precision and durability, which silicone membranes offer. From interior components to protective casings, the reliability of silicone membranes helps in reducing weight while enhancing the performance of aircraft parts.
3. Consumer Products
In the realm of consumer goods, silicone membranes are vital for the production of packaging trays, blister packs, and specialized containers. Their adaptability allows manufacturers to create bespoke solutions catering to various product shapes and sizes.
4. Medical Devices
Silicone's biocompatibility makes it an excellent material for use in medical devices. Vacuum forming a silicone membrane allows the production of customized trays and molds for surgical instruments, ensuring sterility and precision.
Factors to Consider When Choosing a Silicone Membrane
When selecting a suitable silicone membrane for vacuum forming, consider the following factors:
- Application Requirements: Identify the specific needs of your project, including temperature ranges and chemical exposure.
- Membrane Thickness: Assess the appropriate thickness for your application to ensure optimal performance and durability.
- Manufacturer Reputation: Choose a reputable manufacturer with a track record of quality and reliability in silicone production.
- Cost vs. Benefit: Evaluate the cost in relation to the benefits gained. Investing in a high-quality silicone membrane can lead to cost savings in the long run through reduced failure rates and improved product quality.
Maintenance and Care for Silicone Membranes
Proper maintenance and care can significantly extend the lifespan of your silicone membrane for vacuum forming. Follow these tips:
1. Regular Cleaning
Clean the silicone membrane frequently to remove any residues that can accumulate from the vacuum forming process. Use mild detergents and soft cloths to avoid scratching the surface.
2. Inspect for Damage
Regularly inspect the membrane for signs of wear or damage. Address any issues immediately to prevent further degradation that can affect the vacuum forming process.
3. Proper Storage
When not in use, store silicone membranes in a cool, dry environment, free from sharp objects that could puncture or damage the material.
Conclusion: The Future of Silicone Membranes in Vacuum Forming
As technology advances, the demand for high-quality, durable materials continues to grow. The role of silicone membranes for vacuum forming is essential in responding to this demand, providing innovative solutions across various industries. By choosing the right silicone membrane and employing best practices for maintenance, manufacturers can optimize their production processes and enhance the quality of their products.
Why Choose Vacuum-Presses.com for Your Silicone Membrane Needs?
At vacuum-presses.com, we understand the importance of high-quality materials in the vacuum forming process. Our range of silicone membranes has been designed with durability and efficiency in mind, ensuring you have the best tools at your disposal for your manufacturing needs. Our commitment to quality and customer satisfaction sets us apart in the industry.
Contact Us for More Information
If you are interested in learning more about silicone membranes for vacuum forming or have specific requirements, please contact us. Our team of experts is ready to assist you in finding the perfect solution for your business requirements.